flow diagram of crushing plant with 3 crusher open circuit
flow diagram of crushing plant with 3 crusher open circuit
Consultar flow diagram of crushing plant with 3 crusher open circuitThe flow diagram depicts a crushing plant with three crushers operating in an open circuit. The primary crusher receives the raw material and reduces it to a manageable size before it is conveyed to the secondary crusher for further processing. From there, the material is transferred to the tertiary crusher for final reduction before being screened to separate the desired product sizes. This open circuit arrangement allows for efficient material flow and ensures that the crushing process can handle a wide range of input materials. With three crushers working in tandem, the plant can achieve high throughput and consistent product quality. The flow diagram provides a clear visualization of the entire process, making it easier for operators and engineers to understand and optimize the performance of the crushing plant.
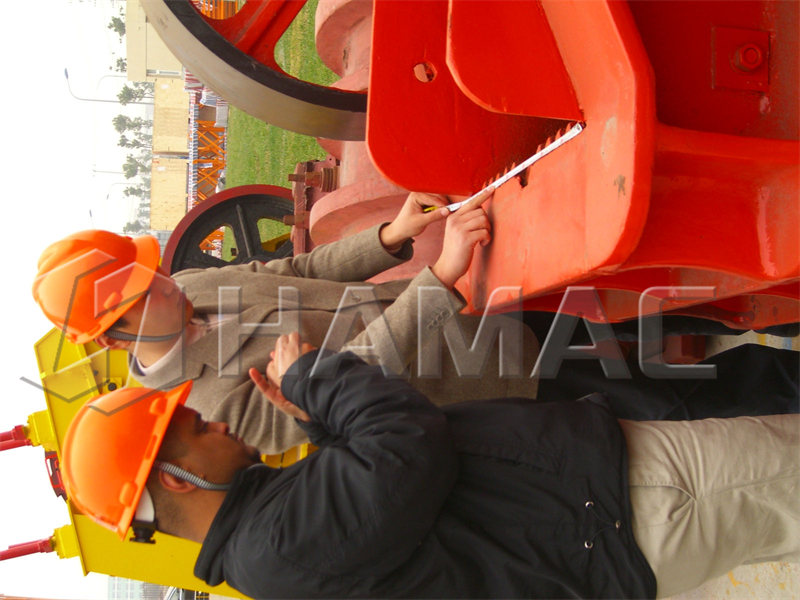
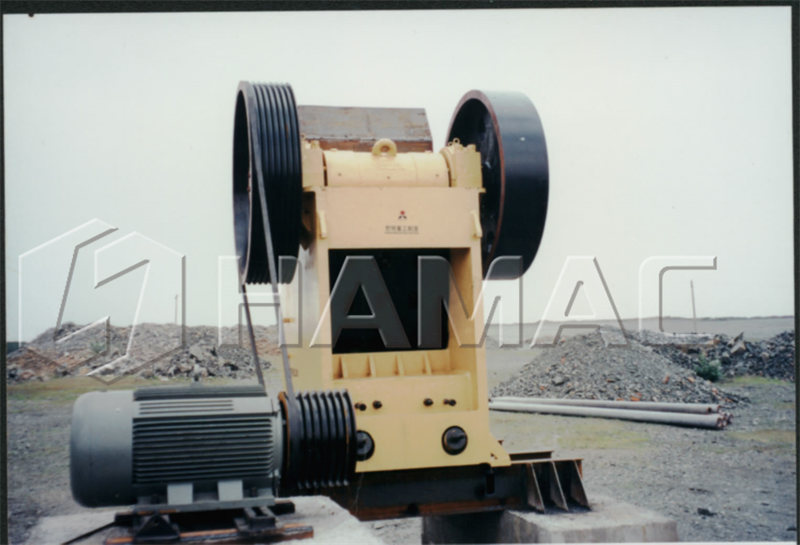
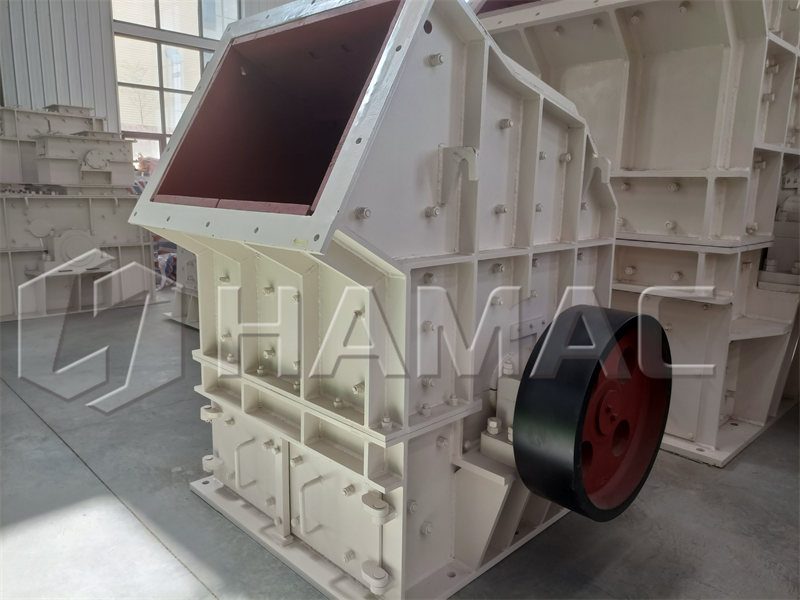
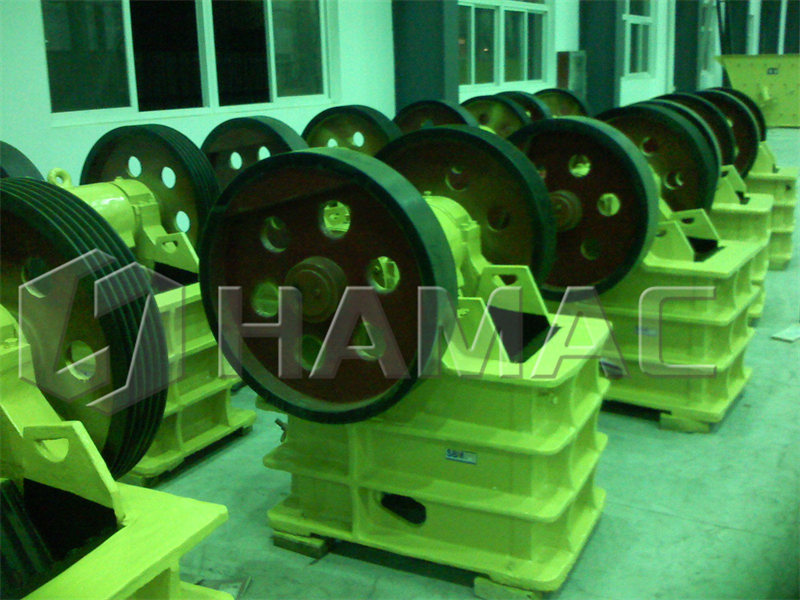
INTRODUCTION
Jaw crushers are often used for primary crushing in mine material crushing. Jaw crusher is an equipment developed for aggregate crushing of highways, railways, airport runways and other engineering constructions. The jaw crusher produced by HAMAC adopts new crushing technology and manufacturing level, and is an ideal product for crushing hard and highly abrasive materials. Compared with the traditional jaw crusher, the HAMAC jaw crusher shows its superiority in terms of service life, maintenance rate and failure rate.
How to select the jaw crusher sizes for your project?
When you want to build a stone crusher plant, there are several important factors to be considered:
1. The maximum stone size before crushing. From this data, the feed opening of jaw crusher can be confirmed;
2. How many tons or cubic meters per hour you want to process?
3. The feeding size of the next crushing stage. The above three factors need to be considered together. The most important factor is the capacity of jaw crusher, even the stone size is smaller, but in order to reach the capacity, you have to choose a bigger jaw crusher. Meanwhile, you also have to consider the output size of jaw crusher, if it is suitable for the secondary crusher or not. It is a complicated stone crusher plant design, please contact our experienced expert to get more support.
Advantages of S series Symons cone crusher
1.Have many types of crushing cavity. The S series cone crusher possess special design, and the customers can choose the type of crushing cavity which has high efficiency, uniform granularity, good shape, uniform abrasion and long use life of bowl liner and mantle. Choose special material to manufacture key assemblies to support large crushing force.
2.High capacity. Compared with other types of spring cone crusher for sale, the series of S cone crusher has longer crush arm, larger stroke, higher crushing force. It can crush the material more efficiently.
3.Every stroke crushes more material.
4.The mantle of S series cone crusher leaves bowl liner further in every stroke, so the crushed material is much more at every stroke, and the materiel pass through the cavity more quickly. As a result, the capacity is increased by many times;
5.Low cost of daily run and maintenance. The component of cone crusher spare parts and structure is better, prolong the use life; the long crush arm to reduce the load of slip bearing, gear, and shell; the granularity of the product is uniform, so the circular load is less; the system of cleaning cavity with hydraulic pressure is convenient , save time, low power and distribution in reason.
Goods Delivery
Based on good quality and decades of experience, the Trailer Concrete Pump which is manufactured by HAMAC was exported to different countries. The Trailer Concrete Pump will be packed and loaded in our factory, and then be shipped to our clients safe and sound.
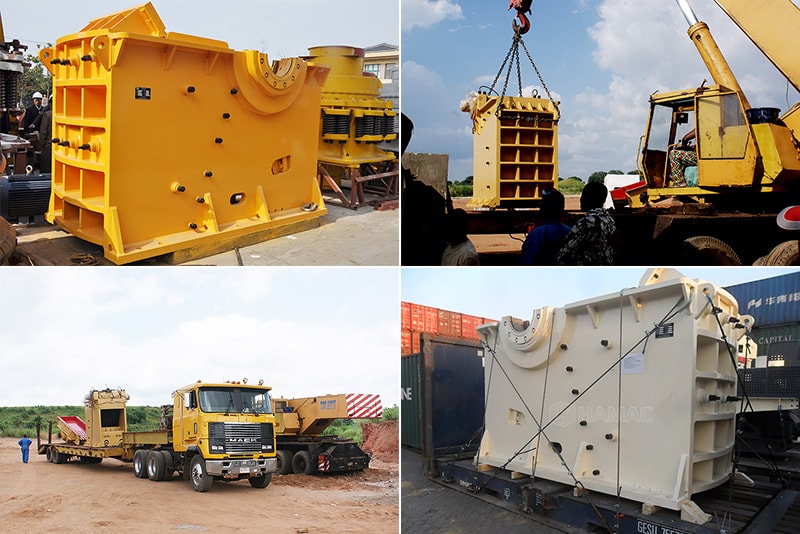