how to manufacture bricks with machines
how to manufacture bricks with machines
Consultar how to manufacture bricks with machinesBrick manufacturing with machines is a modern and efficient process that involves several key steps. First, the clay or shale is crushed and mixed with water to create a malleable mixture. Then, the mixture is shaped into individual bricks using a molding machine, which ensures uniform size and shape. After that, the bricks are dried in a controlled environment to remove excess moisture and improve their strength. Once dried, the bricks are fired in a kiln at high temperatures to harden them and enhance their durability. Finally, the finished bricks are ready for packaging and distribution. Using machines for brick manufacturing offers numerous advantages, including increased production efficiency, consistent quality, and reduced manual labor. Additionally, it allows for the production of a wide range of brick types, sizes, and colors to meet diverse construction needs. Overall, the use of machines in brick manufacturing represents a significant advancement in the industry, offering improved productivity and product quality.
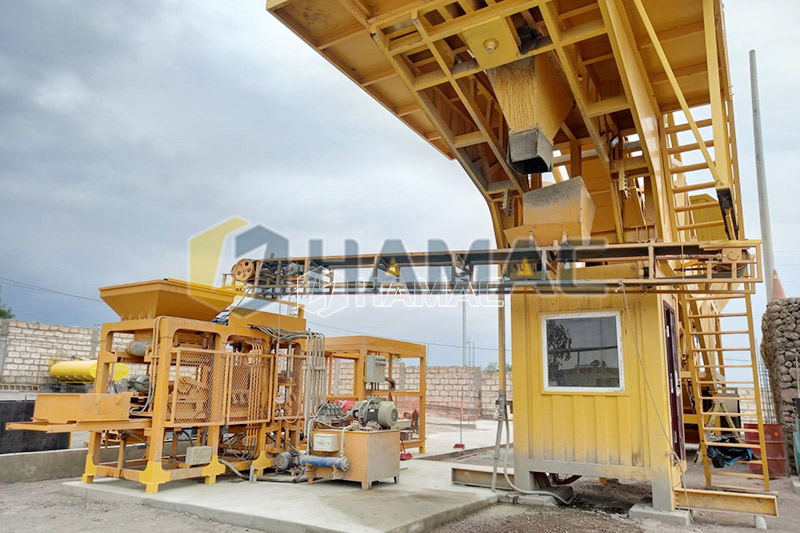
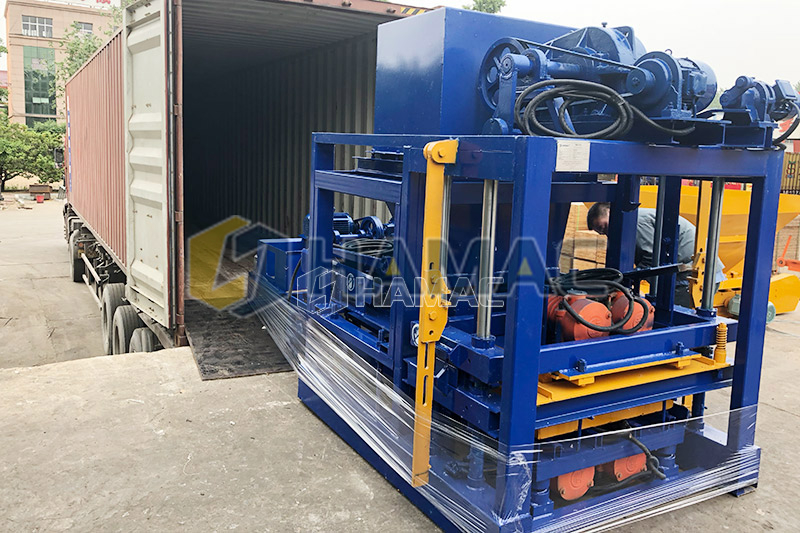
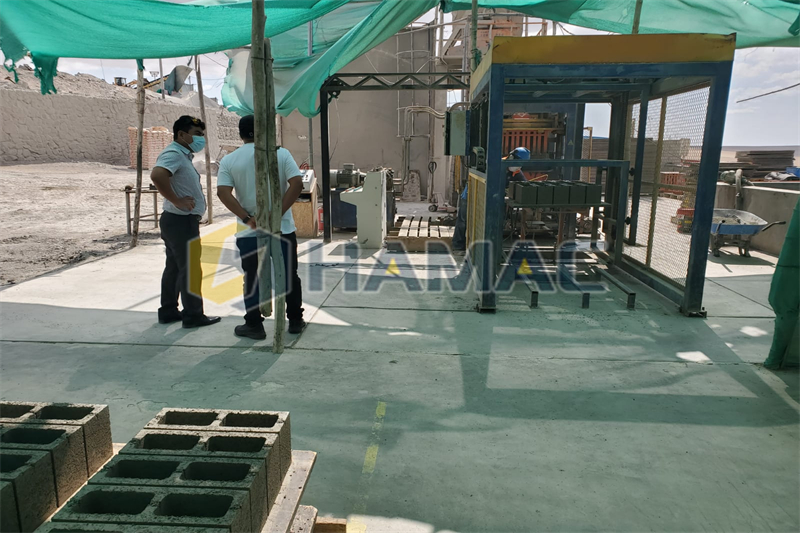
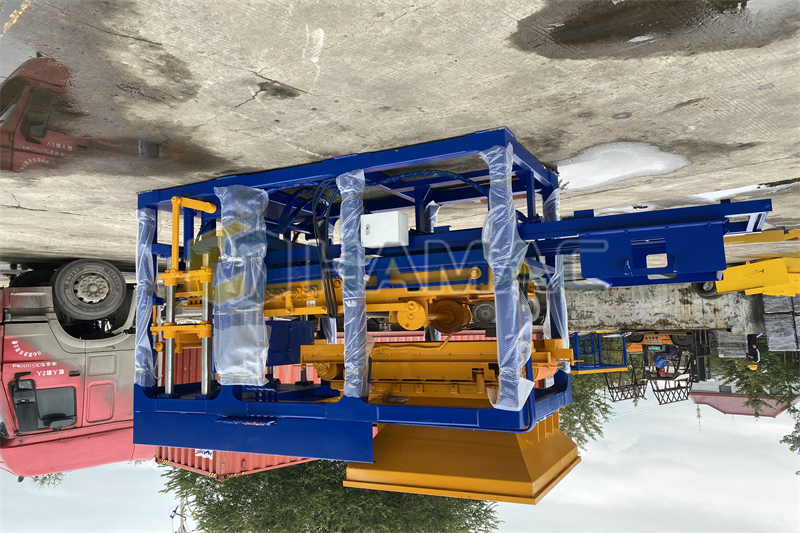
INTRODUCTION
A fully automatic concrete block making machine production line includes aggregate batching machine, JS twin shaft concrete mixer or JQ pan mixer or planetary concrete mixer to produce concrete, concrete block making machine, automatic stacker and pallet feeding machine as options.
Brief introduction of hollow block maker machine
Hollow block machine is the device for producing various hollow blocks and paver bricks. You can just change different molds for different sizes blocks or bricks on the HBM. Then you can produce different blocks and bricks such as: Eco brick, insulating block, hollow block, holes block, solid block; And paver blocks, such as: interlock block, Dutch block, curb; as well as concrete members, dry base brick, planter bricks, fence block for parks, air port and wharf etc.
Types and models of hollow block machine
HAMAC can provide you with egg-laying mobile concrete block machine, manual block machine, semi-automatic concrete block machine and full automatic hydraulic concrete brick making machine for sale as options to produce different hollow block size. There are many different types and models concrete block making machine in the market. According to different standard, we can divide them into different type. Mobile type, also name egg-laying concrete block making machine, it can be moved all the time, and the block is produced on the ground, no need the pallet. It is suitable for some small factories with big working areas;
We can design the hollow block factory for you according to the land you have. We have the working sites in different areas of Philippines. You can visit them for a clear idea.
Different hollow block machine design
According to different factors, we can divided the cement brick machines to many different types
1. Degree of automation, there are automatic cement brick machine, semi-automatic cement brick machine and manual cement brick making machine;
2. Forming principle, there are mechanical vibration cement hollow block machine and hydraulic forming cement hollow block machine for sale;
3. Mobile or stationary, there are mobile concrete hollow block machine and stationary concrete hollow block machine. The mobile type is also named as portable cement hollow block machine or egg laying cement brick machine;
Goods Delivery
Based on good quality and decades of experience, the Trailer Concrete Pump which is manufactured by HAMAC was exported to different countries. The Trailer Concrete Pump will be packed and loaded in our factory, and then be shipped to our clients safe and sound.
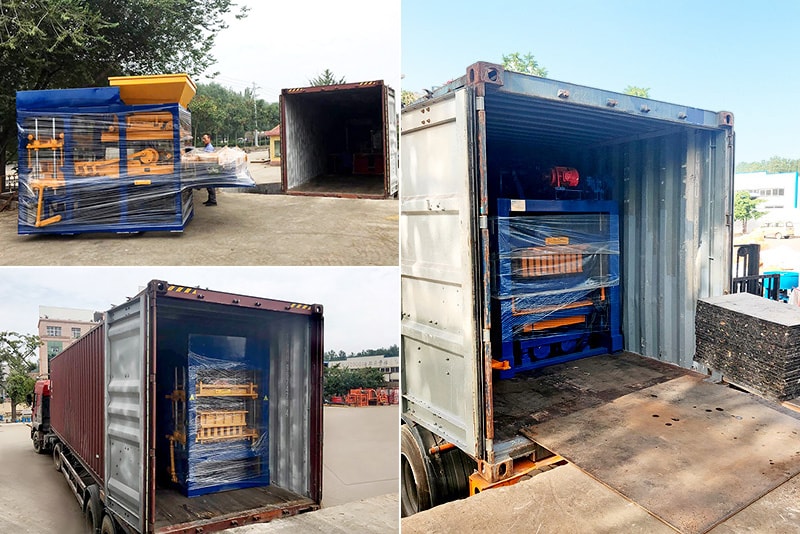